Autoclave Bags
-
Autoclavable Bags: Fruth's autoclave bags offer great impact and puncture resistance, designed to withstand the rigors of steam sterilization.
-
Material: Made of virgin polypropylene, ideal for sterilizing medical tools, instruments, and biohazard waste.
-
Sterilization Compatibility: Suitable for gravity steam, high vacuum steam, ETO gas, and chemical sterilization.
-
Autoclaving Method: Commonly used in the medical industry for sterilizing infectious waste using high-temperature, high-pressure steam for a specific time.
-
Dry Heat Sterilization: For dry heat sterilization, consider Fruth’s nylon sterilization pouches.
-
ISO Certified: Fruth is an ISO 9001:2015 certified manufacturer & distributor of standard and custom autoclave bags and pouches.
-
Product Types: Offers resealable bags, anti-static bags, parts and sample bags, biohazard bags/pouches, and specimen bags/pouches.
-
Regulatory Compliance: Autoclave biohazard bags meet all Federal and State regulations for biohazard waste.
-
Made in the USA: All products are made domestically in the USA.
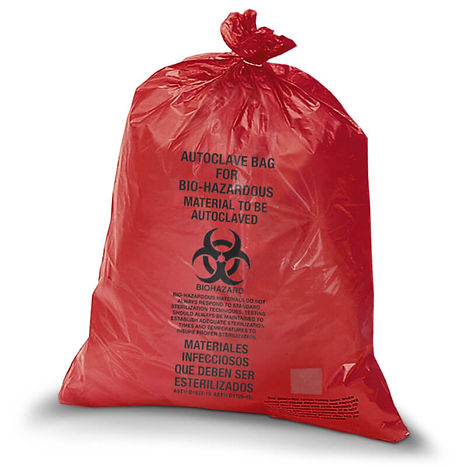.jpg)
Autoclave Packaging Features

-
Used to collect, pack, compile, & dispose of infectious & harmful waste
-
Meets all specifications for autoclaving per USP <1211>
-
Flat or gusset bag – 1.5-6 mil gauge thickness
-
Impact resistance of 165 grams per ASTM D1709
-
Tearing resistance of 480 grams in both MD and TD per ASTM 1922
-
Proprietary inspection process for zero failures in the field
-
Red opaque color to meet biohazard classification requirements
-
Available with or without temperature indicator ink that changes color when conditions for autoclaving have been met
Autoclave Bags in Use
Autoclave Bag Manufacturing
At Fruth Custom Packaging, the manufacturing process of our autoclave bags begins with a vertically integrated approach that allows us to oversee and control every aspect of production. This process starts with the extrusion of high-quality virgin polypropylene, which forms the base material for our bags.
Our state-of-the-art extrusion lines are operated under stringent quality control measures to ensure that the raw materials meet the highest standards for strength and durability, which are crucial for autoclave applications.
Once the extrusion is complete, the material undergoes conversion, where it is shaped, cut, and prepared into bags of various sizes and specifications. Our advanced conversion machinery allows for precise and consistent output, minimizing waste and maximizing efficiency.
This stage also includes critical quality checks to verify that each bag meets our exacting standards for impact and puncture resistance, ensuring they can withstand the rigors of steam sterilization processes.
Customization is the final step in our vertically integrated process, where we tailor the bags to meet specific customer requirements, such as adding resealable closures, anti-static properties, or custom printing for identification purposes.
This comprehensive, integrated approach allows Fruth Custom Packaging to offer unmatched quality control and flexibility, saving our clients time and money while delivering products that provide peace of mind.
As the West Coast’s premier vertically integrated plastic manufacturing facility, we take pride in delivering autoclave bags that not only meet but exceed industry standards.
